Comprehensive Overview: What is Porosity in Welding and Exactly How to Prevent It
Wiki Article
The Scientific Research Behind Porosity: A Comprehensive Overview for Welders and Fabricators
Understanding the detailed systems behind porosity in welding is crucial for welders and makers pursuing remarkable craftsmanship. As metalworkers explore the midsts of this phenomenon, they discover a globe governed by various aspects that influence the formation of these small gaps within welds. From the composition of the base materials to the ins and outs of the welding process itself, a plethora of variables conspire to either aggravate or relieve the presence of porosity. In this comprehensive guide, we will certainly unwind the science behind porosity, exploring its results on weld quality and unveiling advanced methods for its control. Join us on this trip with the microcosm of welding blemishes, where accuracy fulfills understanding in the pursuit of flawless welds.Comprehending Porosity in Welding
FIRST SENTENCE:
Examination of porosity in welding reveals vital insights into the stability and high quality of the weld joint. Porosity, identified by the visibility of cavities or spaces within the weld metal, is an usual worry in welding procedures. These spaces, otherwise effectively addressed, can endanger the architectural stability and mechanical buildings of the weld, resulting in potential failures in the completed item.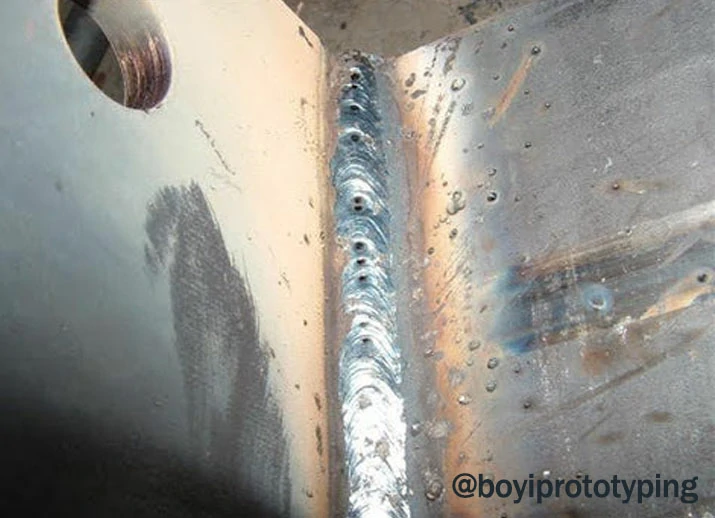
To spot and quantify porosity, non-destructive testing methods such as ultrasonic testing or X-ray inspection are frequently used. These strategies permit the recognition of interior problems without compromising the honesty of the weld. By assessing the dimension, shape, and distribution of porosity within a weld, welders can make enlightened decisions to improve their welding procedures and accomplish sounder weld joints.
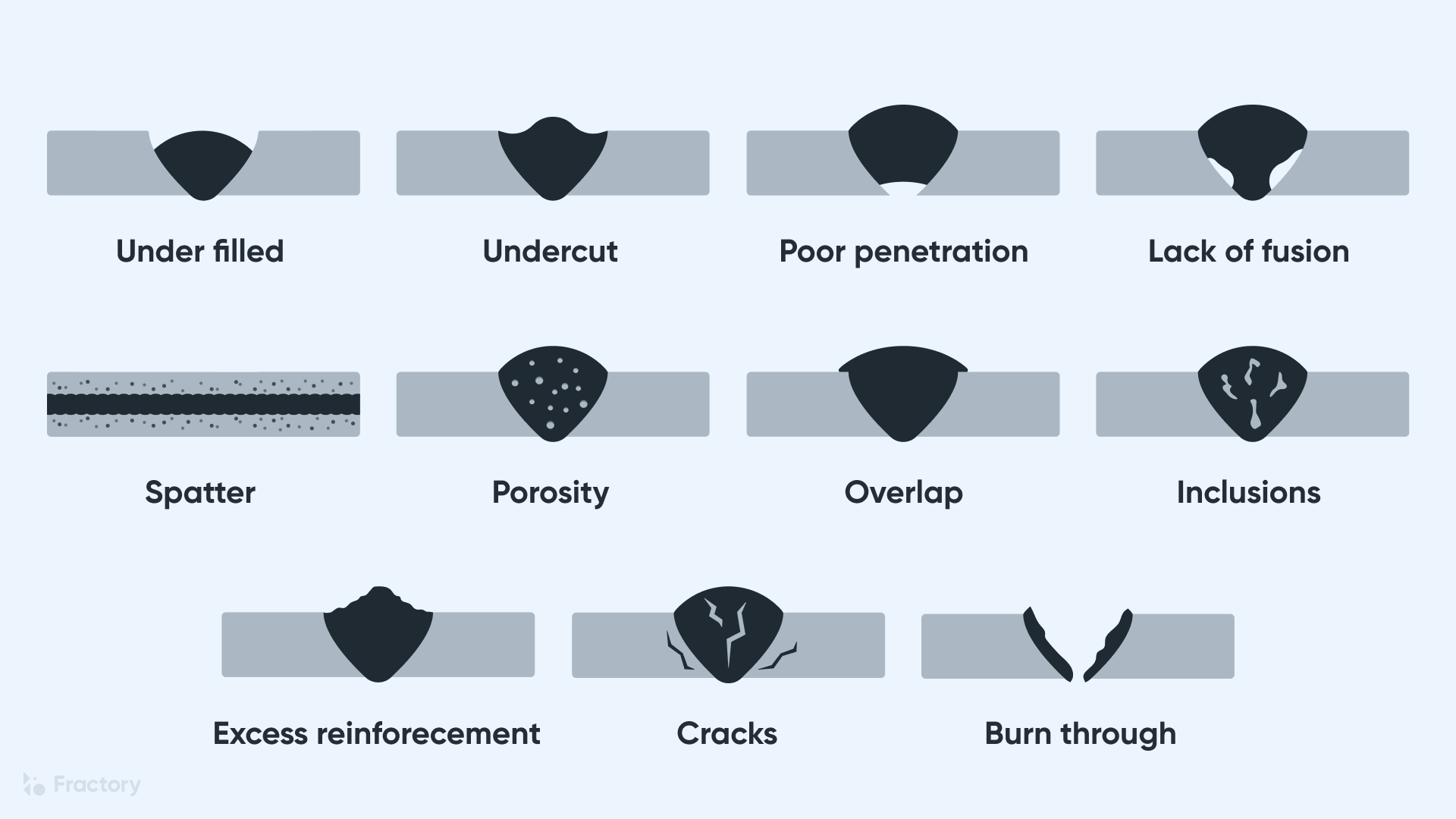
Variables Affecting Porosity Formation
The incident of porosity in welding is influenced by a myriad of elements, ranging from gas shielding efficiency to the complexities of welding specification settings. Welding parameters, including voltage, current, take a trip rate, and electrode kind, likewise effect porosity formation. The welding technique used, such as gas steel arc welding (GMAW) or secured steel arc welding (SMAW), can affect porosity formation due to variants in warm distribution and gas insurance coverage - What is Porosity.Impacts of Porosity on Weld Quality
Porosity development dramatically jeopardizes the structural integrity and mechanical properties of welded joints. When porosity exists in a weld, it creates gaps or cavities within the product, lowering the total stamina of the joint. These gaps serve as tension concentration factors, making the weld more vulnerable to breaking and failure under load. The presence of porosity additionally weakens the weld's resistance to rust, as the trapped air or gases within deep spaces can respond with the surrounding atmosphere, causing deterioration with time. In addition, porosity can hinder the weld's capability to withstand pressure or effect, additional endangering the overall top quality and reliability of the bonded structure. In critical applications such as aerospace, vehicle, or structural building and constructions, where security and resilience are vital, the harmful impacts of porosity on weld quality can have severe consequences, stressing the importance of minimizing porosity via correct welding methods and treatments.Techniques to Decrease Porosity
Additionally, utilizing the ideal welding parameters, such as the correct voltage, present, and take a trip speed, is important read here in stopping porosity. Maintaining a regular arc size and angle throughout welding additionally aids lower the possibility of porosity.
Utilizing the proper welding strategy, such as back-stepping or utilizing a weaving motion, can additionally aid distribute warmth equally and minimize the possibilities of porosity development. By implementing these methods, welders can efficiently lessen porosity and generate top notch welded joints.

Advanced Solutions for Porosity Control
Executing cutting-edge innovations and cutting-edge approaches plays a pivotal role in accomplishing premium control over porosity in welding procedures. One sophisticated service is the usage of advanced gas blends. Shielding gases like helium or a blend of argon and hydrogen can help in reducing porosity by giving much better arc security and enhanced gas protection. Additionally, using innovative welding methods such as pulsed MIG welding or changed ambience welding can additionally aid mitigate porosity concerns.Our site
One more sophisticated solution involves using innovative welding equipment. For instance, making use of devices with built-in features like waveform control and advanced power sources can enhance weld high quality and decrease porosity threats. In addition, the implementation of automated welding systems with exact control over parameters can look at this website considerably decrease porosity defects.
Additionally, integrating innovative monitoring and examination technologies such as real-time X-ray imaging or automated ultrasonic testing can aid in spotting porosity early in the welding process, enabling prompt restorative activities. Overall, integrating these advanced options can greatly boost porosity control and improve the total quality of bonded components.
Final Thought
In conclusion, understanding the scientific research behind porosity in welding is essential for welders and makers to produce high-quality welds - What is Porosity. Advanced remedies for porosity control can better boost the welding process and make certain a solid and trustworthy weld.Report this wiki page